Plant Supervisor
Posted on Feb. 25, 2025 by Haskell Lemon Construction
- Shawnee, United States of America
- $75000.0 - $85000.0
- Full Time
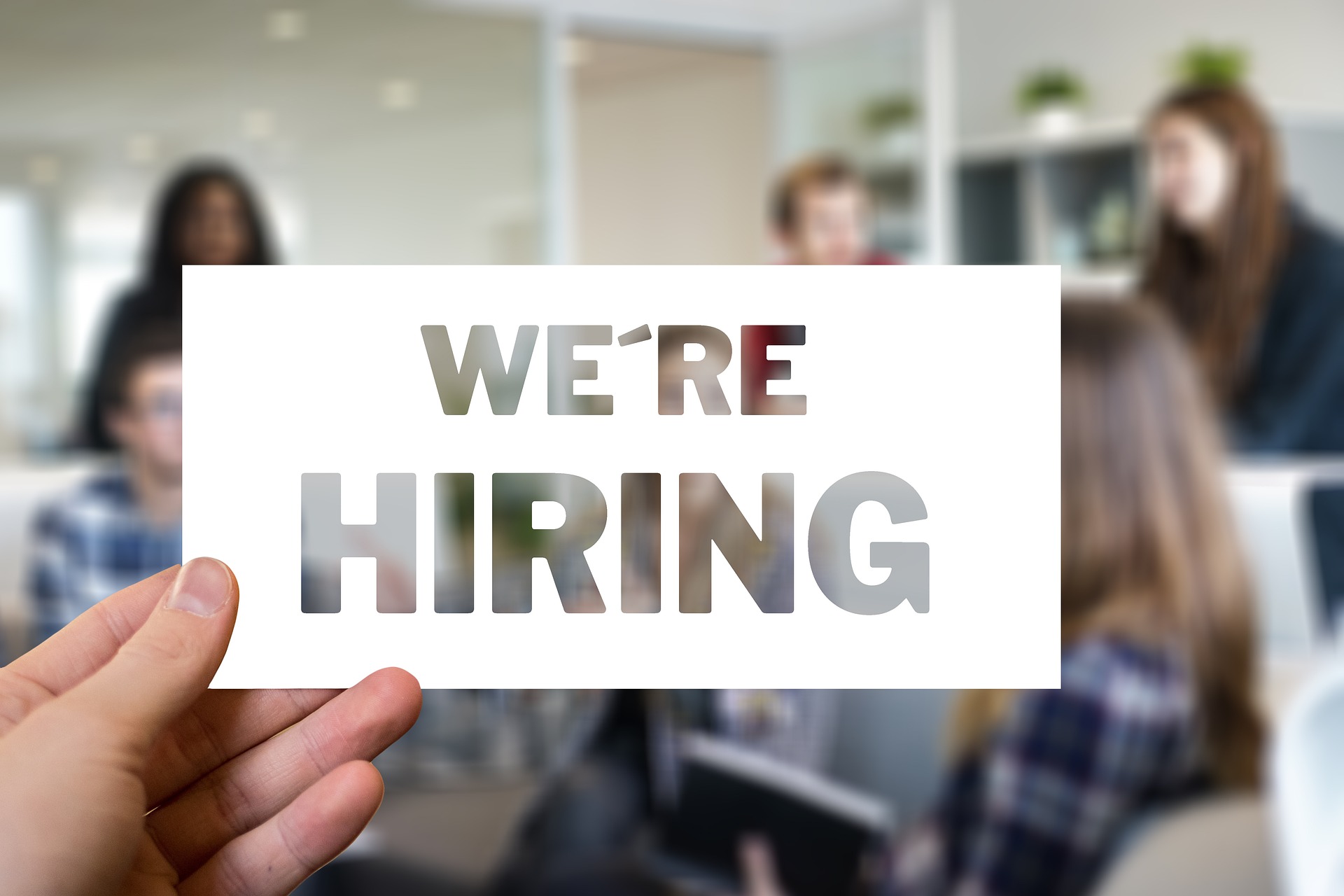
***MUST HAVE ASPHALT PLANT EXPERIENCE***
Haskell Lemon Group, LLC
HLG Plant Manager
Reports to Plant Operations Manager
Job – Key Result Areas (KRA)
1. Effectively Manage all Asphalt Plant Operations o Effectively evaluate your plant and maintain top mechanical condition. o Keep up with daily maintenance needs to keep your plant in good condition at all times. o Work with Human Resources to fill any personnel needs. o Be the leader of your facility in learning & teaching the OCI process. Help teach to your staff what continuous improvement means & how important it is. o Work with your supervisor to have the right size crew. o Work effectively to mentor & train your employees on proper equipment & plant operation. o Work closely with QC to make sure we are making a quality product at all times! o Ensure all employees, contractors, vendors & customers follow all company safety policies. o Manage all material inventory to ensure no delays in production. This includes AC, raw materials, recycle materials, etc. Proper lead time for material ordering is crucial. o Keep up with regular inspections & paperwork requirements for all environmental needs. o Learn all facility functions to be able to operate any aspect of the plant or any other equipment to not only help with production when needed but also be able to train new employees the safe operation of any equipment on the facility. o XBE is a vital tool for our business. Training yourself & your staff how to use this tool is key to our daily success. o Work with central dispatch to ensure we have proper information for each customer. Formulate a plan for production the day prior if possible.
2. Safety o Establish and maintain all operations in a safe and workable situation. o Follow all OSHA regulations and create a culture that maintains a high emphasis on safety practices. o Routinely inspect your facility to ensure proper guarding is in place at all times, no entry zones are marked/communicated, and traffic lanes are abided by. o Insist on clean, organized facilities. o Conduct regular safety meetings as required. o Report all accidents, incidents, injuries to your supervisor and safety director immediately.
3. Create and Maintain the Highest Standards of Plant Operations o Top priority is safety. Continue to lead by example with safe work practices while performing repairs and maintenance & plant operation. Never turn a plant on post repair without the proper safety precautions addressed. o Continue to teach efficiency to all plant employees through maximizing performance of the plant. o Improve communication between the HMA Plant Division. Including coordinating downtime, planned or unplanned repairs. Schedule welders, electricians. Present all repair needs to your supervisor. o Instill pride in all employees to run best of class plants, with innovation, efficiency in mind. o We are very customer oriented. We treat our customers with respect at all times. No exceptions!
4. Produce all Material in Specification and in the most efficient manner. o Evaluate baghouse conditions at your plant to ensure maximum efficiency in accordance with our internal standards. We do not want to be as good as DEQ laws, we want to be significantly better. o Educate yourself and your team with the help of industry professionals. All manufacturers want to help when called upon. o Work with your supervisor to tune burners at your plant. Maximize natural gas consumption. Help review start up and shut down procedures to maximize not only natural gas but electricity and material management as well.
5. Parts and Part Inventory o Identify and list crucial, long lead time items and ensure our inventory availability for these parts. Work with your supervisor to minimize any high-cost items for inventory that are not critical. o Work with your staff to train & understand proper procedures in conducting any maintenance of equipment on facility. Lock out tag out etc. when in doubt contact your supervisor. o Create inspection intervals based on high, medium, and low wear mechanical components at your facility. o Insist on maximum production capabilities for efficiency & safe operation. o Learn and stay the Innovative leader of your facility.
6. Operation Excellence
o Ensure you & your staff represent Haskell Lemon in a professional manner to all customers at all times. o Ensure we always provide the highest quality product; this includes asphalt mixes, customer service, preventative maintenance programs, employee development, management practices. Strive to be the best.
Job Type: Full-time
Pay: $75,000.00 - $85,000.00 per year
Benefits:
- 401(k)
- 401(k) matching
- Dental insurance
- Employee assistance program
- Health insurance
- Life insurance
- Paid time off
- Vision insurance
Supplemental Pay:
- Bonus opportunities
Work Location: In person
Advertised until:
March 27, 2025
Are you Qualified for this Role?
Click Here to Tailor Your Resume to Match this Job
Share with Friends!
Similar Internships
Plant Supervisor
Lead a team of plant operators and technicians. Assign tasks, provide training, and ensure the staf…
WATER AND SEWAGE PLANT SUPERVISOR (CORRECTIONAL FACILITY)
Under the general supervision of the Chief Engineer I, the Water & Sewage Plant Supervisor is r…
Plant Supervisor
Cargill’s size and scale allows us to make a positive impact in the world. Our purpose is to nouris…
Plant Supervisor
Date: 16 Apr 2025 Location: Ulan, NSW, AU, 2850 Company: Orica About Orica At Orica, it’s the…
LPG Plant Supervisor - General Santos City
Are you ready to start your legaSEA? SEAOIL is looking for passionate talents to help make a differ…
ICE PLANT SUPERVISOR
Graduate of any Business course and have at least 1 year experience in the related field.Attention …