Production Manager
Posted on April 2, 2025 by Micrylium Laboratories Inc.
- North York, Canada
- N/A
- Full Time
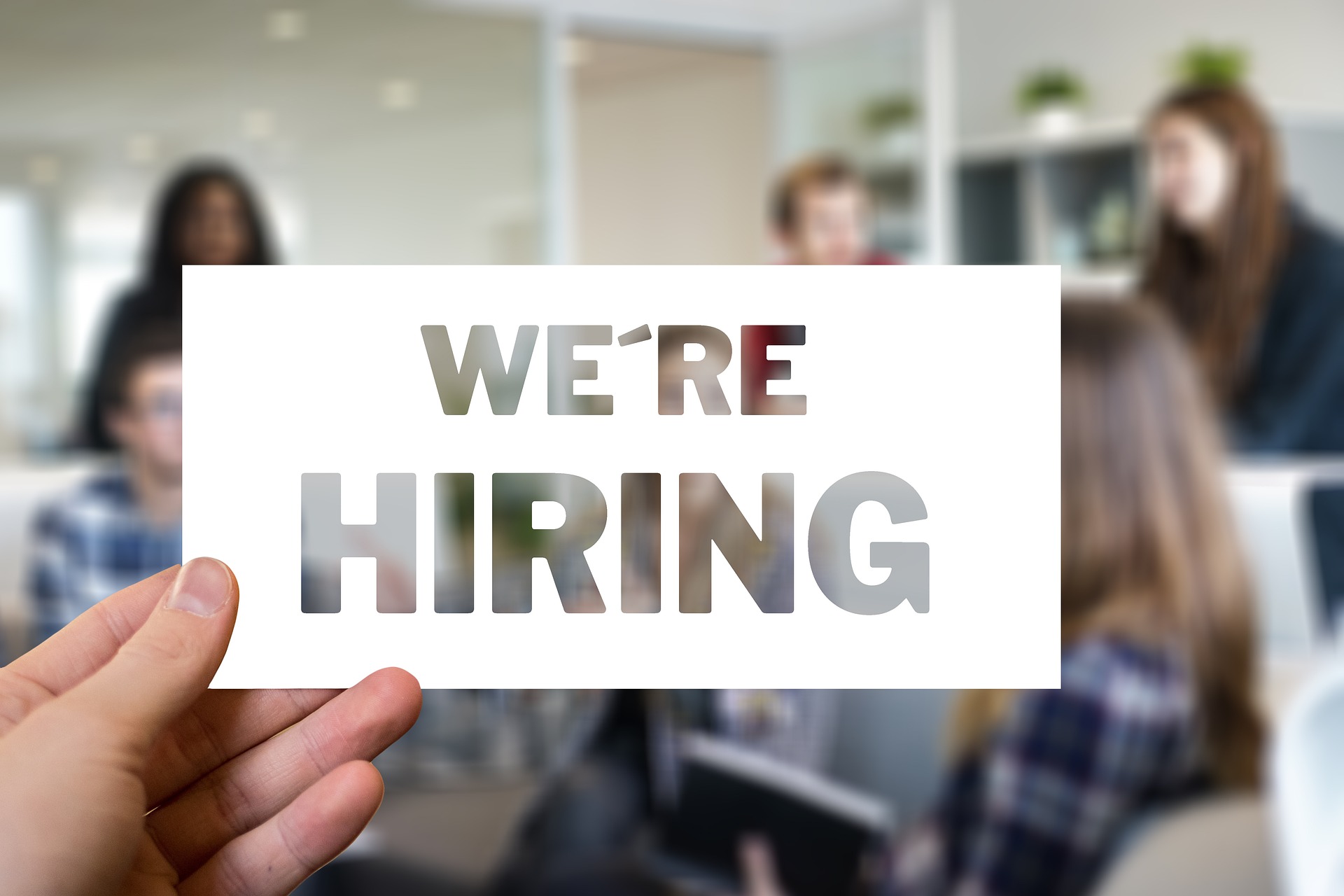
Job Summary
We are seeking a dedicated and experienced Production Manager to oversee our manufacturing operations. The ideal candidate will possess strong mechanical knowledge, experience with welding and metal fabrication and a passion for continuous improvement. This role requires a hands-on approach to managing production processes, ensuring quality control, and optimizing supply chain systems. The Production Manager will lead a team to achieve operational excellence while fostering a culture of safety and efficiency.
Duties
1. Production: Coordinating with the Head Chemist the activities related to batch preparation and execution. Prepare the batch formulas provided that include a list of all components of the dosage form to be used in the manufacturing process, their amounts on a per batch basis, including overages, and a reference to quality standards.
2. Packaging: Establish the production run by setting up the production line, ensuring that staff are fully trained and ergonomically positioned to maximize efficiency. Packaging must maintain strict adherence to keeping the product safe during shipment between the manufacturing facility and the customer and must prevent damage while the product sits on the shelf.
3. Quality Control: Set quality standards for (SOP)production and develop operational processes that use best practices, strict adherence to standards, and specifications to deliver products without defects. Maintain daily quality control to manage costs, reduce waste, and protect the company from brand damage and liability that often accompanies defective products. Report any discrepancies related to quality control immediately to the General Manager.
4. Operational Planning Processes: Establish a weekly and monthly production and packaging schedule in coordination with the Head Chemist and General Manager. Develop operational processes that solve problems. The goal is to have zero backorders.
5. Optimization: Responsible for optimization of machinery updates, maintenance, ergonomic filling and packaging
6. Production Cost Analysis: Establish a measurement/cost analysis process for each production run detailing man hours and material costs per sku. Data will be reviewed and improvements in processing made where necessary.
7. SOPs: Responsible for creating, documenting and maintaining these procedures related to operations in coordination with the President
8. Budgeting: Responsible for input related to the operational budget and executing the effective running of the business according to the budget. Identify and implement expense reduction opportunities designed to meet or exceed our budgets.
9. Operations Staff Management: Responsible for all warehouse and production staff management and training. Perform regular staff appraisals evaluating each team member for efficiency, attitude and ability to perform their duties in keeping with company policies.
10. Facility Management: Perform regular maintenance checks on floors, racking, shipping docks and doors. Cleanliness, functionality and safety must be the top priority.
11. Machinery Maintenance: Maintain all operational equipment including the tow motor, filling, packaging, scales, tank, and water filtration system in good working order.
12. Custom Machinery Fabrication: When necessary to improve productivity or replace a malfunctioning part, create custom parts through a fabrication process.
13. Technical Procurement: In keeping with budget projections or in the case of defective equipment procure technical parts needed.
14. Health, Safety and Security: In conjunction with the President, oversee the programs needed to ensure the safety of all operational staff and other people in the company’s facility. This includes but is not limited to ensuring all team members using equipment are certified to do so, ensure proper safety protocols are in place and adhered to ensure staff receive ongoing safety training as required, ensure all signs and placards are in place. Ensure all cameras are functioning and security access (cards and keys) are controlled for each team member. Monitor compliance for all safety and regulatory bodies FFPA (Fire Protection and Prevention) WHIMIS(Workplace Hazardous Materials Information System), Workman’s Compensation, ISO (International Standards Organization) TDG(Transportation of Dangerous Goods).
15. Freight Management: In correlation with the Customer Service Manager oversee all aspects of freight movements, including selecting carriers/couriers and managing this company expense as a percent of sales.
16. Shipping and Receiving: Ensure staff adhere to policies regarding handling and documentation as outlined in the SOP for all incoming and outgoing shipments. Act as backup in the shipping department, which includes operating the tow motor, shrink wrap and weigh-scale, loading and unloading trucks.
17. Communication: Hold team meetings as required to ensure important information is shared as well as team member feedback is provided to management for continuous improvement
18. Continuous Improvement: Responsible for the ongoing implementation of continuous improvement in operations.
19. Leadership: In Operation fulfill the role of a leader to develop the culture, positive work environment for staff and ensure effective continual training required to ensure everyone is working at their highest potential
20. Participates: Involved in special initiatives and projects as required
Experience
- Welding and metal fabrication experience
- Proven experience in a manufacturing environment, preferably in a leadership role.
- Strong mechanical knowledge with the ability to troubleshoot equipment issues effectively.
- Familiarity with Continuous Improvement methodologies, including Lean manufacturing techniques.
- Demonstrated ability in quality control processes and supply chain management.
- Excellent communication skills with the ability to motivate and lead a diverse team.
Join us as we strive for excellence in our production processes while fostering an environment of growth and innovation.
Job Types: Full-time, Permanent
Pay: $60,000.00-$65,000.00 per year
Benefits:
- Dental care
Flexible language requirement:
- French not required
Schedule:
- Monday to Friday
- Weekends as needed
Licence/Certification:
- Welding license (required)
Work Location: In person
Advertised until:
May 2, 2025
Are you Qualified for this Role?
Click Here to Tailor Your Resume to Match this Job
Share with Friends!
Similar Internships
Production Manager
Please note that while we appreciate everyone's interest in working with us, only those with at lea…
Production Manager (Freelance)
Hi, we're Fever We're excited you are checking out this job offer. We are the leading global live-…
Manager Preprocessing (Production Manager)
Rotterdam €4700,-/ €7600,- Vast Als Manager Preprocessing op de Maasvlakte adviseer je a…
Production Manager Packaging Semi-solids
Bonjour. Nous sommes Haleon. Une nouvelle entreprise leader mondial dans le domaine de la sant&eacu…
Event Production Manager
Grand Bazaar NYC Market Production Manager - INTERIMFounded in the late 1970s as GreenFlea by tenac…
DUTY PRODUCTION MANAGER
City: Stockholm-Arlanda Job Function: Other Duty Production Manager - Maintenance Production P145 S…